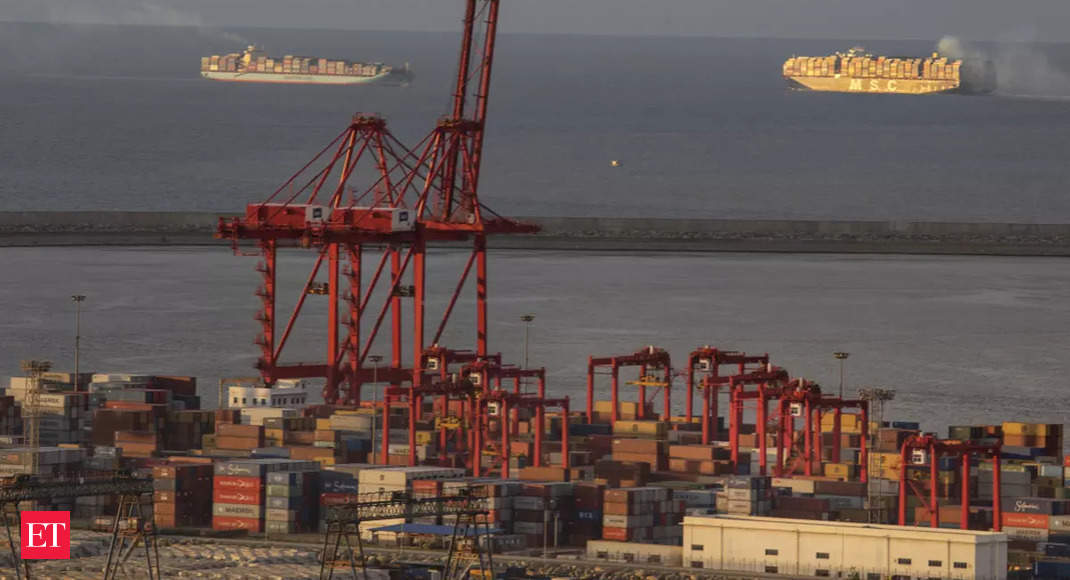
When the pandemic struck in early 2020, people and businesses were quickly forced to restrict their activity, sending the global economy into a brief but damaging free fall.
As offices closed and factories halted production, companies laid off workers en masse, taking spending power out of people’s hands. With fewer goods being made and fewer people with paychecks to spend, companies assumed that demand would drop sharply. But a far more complicated situation unfolded, challenging the global supply chain.
In early 2020, the entire planet suddenly needed surgical masks and other protective gear. Most of it was made in China, which produced half of all protective masks the year before. As factories ramped up to meet the new demand, cargo vessels delivered protective gear around the globe, even to regions that do relatively little trade with China, such as West Africa.
Empty shipping containers piled up in many parts of the world. The result was a shortage of containers in the one country that needed them the most: China.
China’s factories pumped out goods in record volumes. Despite the worry that economic devastation would destroy spending, the pandemic merely shifted the demand: Instead of eating out and attending events, Americans bought office furniture, electronics and kitchen appliances.
The pandemic sharply accelerated the shift toward online shopping, a trend that had been advancing for years. From April to June 2020, as the first wave of the virus spread, Amazon sold 57% more items than it had a year earlier.
The spending in the United States was also encouraged by government relief programs that mailed checks to households, part of a record-setting effort to resuscitate the economy.
As demand increased, a wave of goods swiftly overwhelmed U.S. ports. With too many ships arriving at once, boats sometimes had to wait in 100-vessel queues off the ports of Los Angeles and Long Beach in California. Swelling orders also outstripped the availability of shipping containers, and the cost of sending one from Shanghai to Los Angeles skyrocketed tenfold.
Once unloaded, many containers piled up on docks unclaimed because of a shortage of truck drivers needed to haul cargo to warehouses. Truck drivers had long been scarce before the pandemic, with wages steadily eroding amid grueling working conditions.
Businesses across the economy struggled to hire workers: at warehouses, at retailers, at construction companies and for other skilled trades. Even as employers resorted to lifting wages, labor shortages persisted, worsening the scarcity of goods.
Shortages of one thing turned into shortages of others. A dearth of computer chips, for example, forced major automakers to cut production, while even delaying the manufacture of medical devices.
Businesses and consumers reacted to shortages by ordering earlier and extra, especially before the year-end holidays. That placed more strain on the system.
The crisis has roots in a production model pioneered by Toyota at the end of World War II. Under the model, called “just in time” manufacturing, companies stockpile as few raw materials and parts as possible, instead buying what they need as they need it.
That works only when they can get what they need when they need it. For years, some experts have warned that the global economy is overly reliant on lean production and faraway factories, exposed to the inevitable shock. The pandemic has seemingly validated that view.
How the global supply chain crisis unfolded this year - Economic Times
Read More
No comments:
Post a Comment